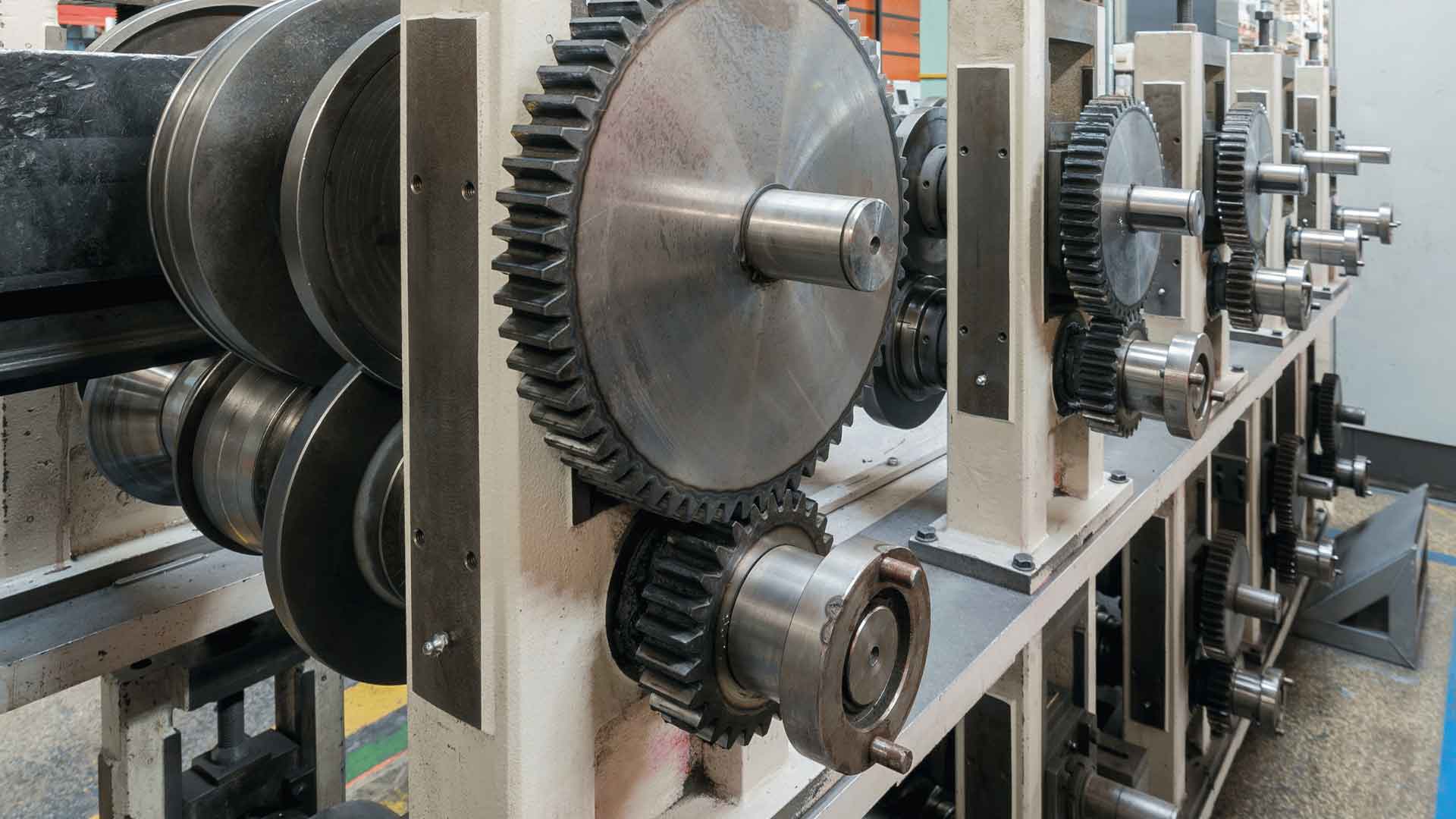
Roll Form Tooling:
Understanding Roll Forming Machines:
Roll forming machines play a crucial role in the manufacturing industry, particularly in the production of metal components with precise and consistent shapes. But what exactly is a roll forming machine, and how does it work? Let’s dive into the roll forming process and explore the intricacies of these powerful machines.
What is a Roll Forming Machine?
A roll forming machine is a specialized piece of equipment designed to transform flat sheet metal into specific, continuous shapes. The machine works by passing the metal through a series of hardened steel rollers. Each roller station gradually bends and shapes the metal, allowing it to form the desired profile by the time it exits the machine. The continuous nature of this process makes it ideal for high-volume production, producing parts efficiently and with minimal waste.
The Roll Forming Process
The roll forming process begins with a flat sheet or coiled strip of metal. This material is fed into the roll forming machine, where it encounters the first set of rollers. As the metal progresses through each subsequent set of rollers, it undergoes small, incremental changes in shape. This gradual shaping minimizes stress on any single part of the metal, reducing the risk of defects or structural weaknesses.
The beauty of roll forming lies in its ability to create complex shapes while maintaining the integrity of the material. From simple corrugated panels to intricate closed profiles, the process is versatile and precise. The metal can be shaped into symmetrical or asymmetrical profiles, depending on the design of the roller dies.
Customization with Roll Forming Roller Dies
Roll forming roller dies are the heart of the machine, dictating the final shape of the metal. These dies are custom-made for each specific job, ensuring that the resulting profiles meet the exact specifications required by the application. Each roller die station may have a unique configuration, contributing to the progressive bending and shaping of the metal.
One of the significant advantages of roll forming is its ability to produce straight profiles with high strength and rigidity. These profiles are commonly used in industries such as manufacturing, commercial construction, aerospace, and more. Materials ranging from aluminum to 6-gauge steel (up to 1/2″ thick) can be processed, highlighting the versatility of roll forming machines.
Additional Operations and Enhancements
Roll forming machines can be equipped with additional features to enhance the final product. For instance, pre-punching operations allow for the precise placement of holes in the metal, which can be used for mounting or weight reduction. Notching is another operation that can create openings or partially remove sections of the metal.
To further optimize the production process, many roll forming machines include a “Flying Cut-Off” mechanism. This allows the metal to be cut to the desired length while it is still moving through the machine, significantly increasing throughput and efficiency.
Conclusion
Roll forming machines are indispensable tools in modern manufacturing, enabling the production of metal parts with high precision and efficiency. By understanding the roll forming process and the role of customized roller dies, we can appreciate the intricate work that goes into shaping metal into the profiles we see in various applications today. Whether in construction, aerospace, or other industries, the capabilities of roll forming machines continue to expand, driving innovation and progress in metal fabrication.