Roll Forming Machines
Excellence in Every Detail
Roll Forming Machine Manufucturer
Cutting-Edge Techniques for Every Profile
Evolutionary Techniques for Every Profile
Adaptable System Designs with Optimized Quality Standards
Experience unparalleled flexibility with system concepts designed to meet the highest quality standards. For decades, our latest roll forming machines and innovative systems have set the benchmark in the industry. As pioneers in roll forming technology, we stand among the world's market leaders. In Turkey, our expertise in roll forming machines ensures you benefit from extensive know-how and adaptable concepts tailored precisely to your needs.
Ideal Choice for M Profile, J Profile, U Profile, and Gypsum Corner Bead Production: Roll Forming Machines
Roll forming machines are industrial machines used for the mass and precise production of various metal profiles such as M profiles, J profiles, U profiles, and gypsum corner beads. Thanks to these machines, profiles with different thicknesses and dimensions can be obtained with desired tolerances and at high production speeds.
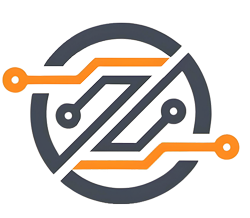
Roll Forming Machines for Medium and Heavy Profiles
Our system concept offers exceptional flexibility to meet your specific roll forming requirements. A standout feature is the rapid tool change, providing you with a significant competitive edge. The consistent design of the P3 series ensures compatibility, allowing you to use our machine components across a wide range of machines, regardless of their age or size.
General Units of Our Rollform Lines
-
Entry Coil Car
-
Uncoiler
-
Straightener (for thick materials)
-
Press Feeder (for perforated profiles)
-
Press
- Mechanical
- Hydraulic
-
Rollforming Machine
-
Cutting Unit
- Flying Saw (hot or cold cutting)
- Flying Die
-
Exit Conveyor
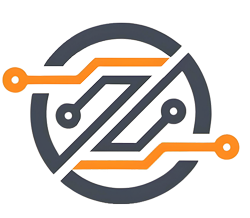
Roll Forming Machines for Thin-Walled Precision Profiles
Our roll forming machines provide an impressive array of applications, from foam-filled aluminum roller blinds and Venetian blinds to welded glass spacers for double glazing. This versatile roll forming machine accommodates three different types of frames and can integrate additional processes such as foaming, punching, and welding. Ready-to-use tool cassettes ensure quick and easy tool changes, allowing your production to resume immediately after a product change."
The Light Steel Profile Production Line is an advanced technology system designed for the production of high-quality steel profiles used in the construction and industrial sectors. This production line is optimized for the precise shaping, cutting, and processing of steel profiles.
Features and Advantages
High Efficiency: The light steel profile production line ensures fast and uninterrupted production, leading to significant time savings and cost-effectiveness in the manufacturing process.
Quality and Precision: Our production line operates with high precision, producing profiles of excellent quality. This enhances the reliability and durability of your products.
Flexibility: The system can be adapted to produce different types and sizes of profiles, allowing you to meet the diverse needs of your customers.
Automation: With fully automated systems and CNC-controlled machines, human error is minimized, making the production process more reliable and consistent.
General Units of Our Rollform Lines
-
Entry Coil Car
-
Uncoiler
-
Straightener (for thick materials)
-
Press Feeder (for perforated profiles)
-
Press
- Mechanical
- Hydraulic
-
Rollforming Machine
-
Cutting Unit
- Flying Saw (hot or cold cutting)
- Flying Die
-
Exit Conveyor

High
Efficiency

Quality and
Precision

Flexibility

Automation
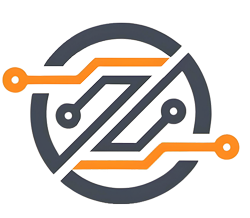
Mold Manufacturing
The most critical and essential aspect of roll forming technology is the design of rollform molds, which are specially designed and analyzed in a computer environment according to the required profile. The mold design data is provided to you as a project file upon completion. Contact us for the most suitable mold design for your specific profile needs.
Design: The process begins with the precise design of the mold, which must meet the specifications of the final product. This includes considering factors such as material flow, cooling, and ejection systems.
Material Selection: The choice of material for the mold is crucial, as it must withstand the stresses of the production process and maintain durability over time.
Machining: Advanced machining techniques, such as CNC milling and EDM (Electrical Discharge Machining), are used to create the detailed features of the mold.
Assembly: After machining, the various components of the mold are assembled and fitted together to ensure proper function.
Testing: The mold is tested with the actual material it will shape to ensure it performs correctly and produces parts to the required specifications.
Adjustment and Finishing: Any necessary adjustments are made to the mold, and finishing touches are applied to ensure smooth operation and a high-quality final product.
Mold manufacturing is critical in industries such as automotive, aerospace, electronics, and consumer goods, where precision and quality are paramount.
The design of rollform molds, which is the most critical and attention-demanding aspect of rollform technology, is carried out and analyzed in a computer environment based on the required profile. By correctly designing and analyzing the bending molds, we apply the necessary manufacturing processes to enhance the strength of the metal. These processes include heat treatment, hole grinding, wire erosion, and CNC turning.
By implementing these processes, we ensure that you can operate smoothly for many years, even within the tightest tolerances.

Design

Machining

Assembly

Finishing
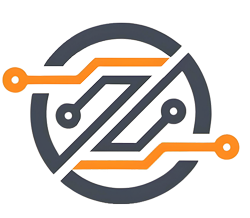
Key Features
- The operator manages the machine via a 19-inch touch-screen industrial computer integrated into the control panel. Remote access to the machines is possible through network and internet connectivity.
- Tasks such as forming profiles from flat sheets, cutting profiles to specified lengths, making service or rivet holes, profile back notching, and profile narrowing are all executed within the drive unit and hydraulic stations using a computer-controlled system.
- The machine operates fully automatically, with the option for the operator to pause and resume production at any time. The production speed can also be modified while the machine is in operation.
- The panel machine is automatically fed with galvanized steel from the uncoiler.
- The machines are designed for easy transportation, and the setup time in the factory is minimal.
- Our quality management and other systems are certified to ensure that the profiles and assembly processes meet industry standards.
Uncoiler Features
- Capable of handling raw materials up to 2500 KG.
- Offers a smooth start/stop operation with electronic control.
- Adjustable speed settings.
- Reversible direction control.
Design Software
- Our software is a robust, adaptable, and user-friendly solution specifically developed for light steel structure systems. It supports the design of various structures, from single-family homes to multi-story buildings or structures with varying floor levels.
- Intuitive 3D graphical interface.
- Geometric tools for support.
- Visualization of production processes, cladding, and 3D structural perspectives.
- Capability to import DXF files.
- Automatically generate the entire structure with the "Autocreate" function.
- Convert 2D architectural drawings or axis lines into 3D structures.
- Perform checks for clashes between profiles and panels, verify panel geometry, and ensure profiles are within maximum length limits.
- Input material properties, load combinations, and load values for analysis purposes.
- View analysis results, including support reactions, deflection checks, and force diagrams.
- Export output in DXF format.
- Generate material reports.
- Output in DXF format in both 3D or plan views.
- Export SAP2000 files.
- Generate arc production files.
- Generate mobile viewing output.
Production Software
-
- After designing in the design program, a production file is created, which is then uploaded to the machine for fully automated production of all parts.
- The production software is Windows-based and easy to use, displaying processed profiles (blue), profiles currently being processed (red), and profiles awaiting processing (gray) as real-time graphics with smart color coding.
- User settings allow adjustments to station processing times, license uploads, and language preferences.
- System settings enable control of station positions, printer configurations, addition or removal of stations, and monitoring of temperature and pressure values, along with tracking and resetting station usage.
- The production section allows for the adjustment of production speed, execution of automatic or manual production, and monitoring of steel consumption, the number of rivets required, production time remaining, and temperature and pressure values during production.
- Length and station calibrations can be performed in the calibration settings.
- The reporting section provides access to production reports, error logs, and station usage statistics.
- The simulation mode allows users to simulate all potential operations on the profile and view the outcomes without conducting actual production.